انواع روشهای سختکاری فلزات: بررسی کامل فرآیندها، مزایا و کاربردها
فلزات بهصورت طبیعی انواع روش های سخت کاری فلزات دارای ویژگیهای مکانیکی مختلفی هستند؛ اما بسیاری از آنها نیاز به تقویت مقاومت سطحی و افزایش سختی دارند تا بتوانند در محیطهای پرتنش، سایشی یا دمایی عملکرد بهتری داشته باشند. سختکاری (Hardening) یکی از مهمترین فرآیندهای مهندسی مواد برای افزایش استحکام و مقاومت به سایش فلزات است. با استفاده از روشهای مختلف سختکاری میتوان خواص سطحی فلزات را بهگونهای بهبود داد که بدون تأثیر زیاد بر خواص درونی، عملکرد و طول عمر قطعه بهشدت افزایش یابد.
در این مقاله، به بررسی کامل انواع روشهای سختکاری فلزات میپردازیم؛ از روشهای حرارتی کلاسیک گرفته تا روشهای نوین سطحی و پیشرفته.
انواع روش های سخت کاری فلزات
الف) کوئنچ و تمپر (Quenching and Tempering)
یکی از رایجترین روشها برای سختکاری فولاد، عملیات حرارتی انواع روش های سخت کاری فلزات شامل گرمکردن تا دمای بحرانی (حدود 800–950°C) و سپس سردکردن سریع در آب، روغن یا هوا است. این فرآیند ساختار فولاد را از پرلیت به مارتنزیت تبدیل میکند و موجب افزایش سختی میشود.
مزایا: افزایش استحکام و سختی
معایب: احتمال ترک یا تاببرداشتن در صورت سردکردن نادرست
کاربرد: قطعات مکانیکی، ابزارآلات، چرخدندهها، شفتها
ب) نرمالهسازی (Normalizing)
در این روش، قطعه تا دمای بالا گرم و در هوا سرد میشود تا ساختار یکنواخت و سختی متوسط حاصل گردد. سختی به اندازه کوئنچ نیست، اما چقرمگی و یکنواختی ساختار بهتر است.
سختکاری سطحی (Surface Hardening)
در بسیاری از کاربردها، تنها سختی سطح اهمیت دارد و مغز قطعه باید چقرمگ باقی بماند. در این موارد از روشهای سختکاری سطحی استفاده میشود.
الف) سختکاری القایی (Induction Hardening)
در این روش، از القای الکترومغناطیسی برای گرمکردن سریع سطح فلز استفاده میشود، سپس سطح به سرعت سرد میگردد. این روش معمولاً برای فولادهای کربنی و آلیاژی کاربرد دارد.
مزایا: سرعت بالا، کنترل انواع روش های سخت کاری فلزات عمق سختکاری
معایب: نیاز به تجهیزات تخصصی
کاربرد: دندهها، میللنگ، غلطکها
ب) سختکاری شعلهای (Flame Hardening)
مزایا: مناسب برای قطعات با سطح بزرگ
معایب: سختی کنترل فرآیند، یکنواختی کمتر
کاربرد: راهنماهای ماشینآلات سنگین، انواع روش های سخت کاری فلزات دندههای صنعتی بزرگ
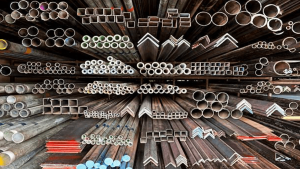
. سختکاری شیمیایی (Chemical Hardening)
در این نوع فرآیند، اتمهایی مانند کربن، نیتروژن یا بور به سطح فلز نفوذ میکنند و با تغییر ساختار سطحی، سختی را افزایش میدهند.
الف) کربوراسیون (Carburizing)
کربن به سطح فولاد افزوده میشود (در محیط جامد، مایع یا گاز)، سپس عملیات انواع روش های سخت کاری فلزات حرارتی انجام میشود تا ساختار مارتنزیتی در سطح ایجاد گردد.
مزایا: سطح بسیار سخت، مغز نرم و چقرمه
معایب: زمانبر
کاربرد: چرخدندهها، پینها، یاتاقانها
ب) نیتراسیون (Nitriding)
در این روش، نیتروژن به سطح فولاد افزوده میشود (معمولاً در دمای پایینتر از کربوراسیون). سختی بسیار بالا و مقاومت به خوردگی نیز حاصل میشود.
مزایا: بدون نیاز به سردکردن سریع، اعوجاج کم
معایب: نیاز به فولادهای خاص آلیاژی
کاربرد: میلبادامک، اجزای موتور، قالبهای دقیق
پ) بوردهی (Boriding)
اضافهکردن بور به سطح فلز باعث ایجاد لایهای بسیار سخت و مقاوم در برابر انواع روش های سخت کاری فلزات سایش میشود. معمولاً در محیط پودری انجام میشود.
مزایا: مقاومت بالا به سایش و خوردگی
معایب: هزینه بالا، تغییر رنگ سطح
کاربرد: تجهیزات حفاری، ابزار برش، قطعات موتوری
سختکاری سرد (Cold Working / Work Hardening)
در این فرآیند مکانیکی، با تغییر شکل پلاستیک فلز در دمای محیط (مانند نورد سرد، کشش یا پانچ)، چگالی نابجاییها افزایش مییابد و سختی فلز بیشتر میشود.
مزایا: عدم نیاز به حرارت، ساختار ریزدانه
معایب: کاهش چقرمگی، احتمال ترک
کاربرد: ورقهای فولادی، مفتولها، قطعات پرسکاری شده
سختکاری لیزری (Laser Hardening)
یک روش مدرن که در آن سطح فلز با تابش پرتو لیزر بهصورت موضعی انواع روش های سخت کاری فلزات حرارت داده میشود. این روش دقیق، کنترلپذیر و بدون تماس است.
مزایا: دقت بالا، تغییر شکل کم، سرعت بالا
معایب: هزینه تجهیزات، نیاز به اپراتور حرفهای
کاربرد: قطعات دقیق ماشینآلات، تجهیزات پزشکی، قالبسازی
سختکاری پلاسما (Plasma Nitriding)
در این روش از تخلیه الکتریکی (پلاسما) در محیط گازی استفاده میشود تا نیتروژن به سطح فلز نفوذ کند. این روش نسبت به نیتراسیون سنتی، سرعت و یکنواختی بیشتری دارد.
مزایا: سازگاری با قطعات پیچیده، کنترل دقیق
معایب: نیاز به تجهیزات تخصصی گرانقیمت
کاربرد: صنایع هوافضا، تجهیزات پزشکی و قطعات دقیق
مقایسه کلی روشها
روش سختکاری نوع فرآیند عمق انواع روش های سخت کاری فلزات سختی تغییر شکل مناسب برای
کوئنچ و تمپر حرارتی زیاد زیاد فولادهای کربنی
سختکاری القایی سطحی-حرارتی کنترلشده کم قطعات گرد یا یکنواخت
نیتراسیون شیمیایی کم تا متوسط بسیار کم قطعات دقیق با آلیاژ بالا
کربوراسیون شیمیایی زیاد متوسط قطعات سایشی
سختکاری سرد مکانیکی سطحی زیاد ورقها و مفتولها
لیزری سطحی-نوین دقیق بسیار کم قطعات دقیق
نتیجهگیری
انتخاب روش مناسب برای سختکاری فلزات به عوامل متعددی بستگی دارد؛ از جمله نوع فلز پایه، شرایط کاری قطعه، دمای کاری، هزینههای تولید، و میزان سختی مورد نیاز. روشهای سنتی مانند کوئنچ و تمپر هنوز هم پرکاربرد هستند، اما با پیشرفت فناوری، روشهای نوین مانند سختکاری لیزری و پلاسما در حال جایگزینی برای قطعات دقیقتر و حساستر هستند.
برای انتخاب صحیح، لازم است کارشناسان و مهندسان متالورژی، نیاز پروژه را با ویژگیهای هر روش تطبیق داده و بهترین گزینه را انتخاب کنند.