تولید کنندگان فولاد فولاد آلیاژی است که از ترکیب آهن و درصدی کربن با عناصری مانند کروم، نیکل، مولیبدن و غیره به دست می آید. این آلیاژ به دلیل خواص خارق العاده ای مانند استحکام کششی بسیار بالا، مقاومت در برابر خوردگی، چکش خواری و انعطاف پذیری به یکی از پرکاربردترین فلزات در جهان تبدیل شده است. این آلیاژ در صورت ترکیب با سایر عناصر و عملیات حرارتی، خواص مناسبی برای هر کاربرد پیدا می کند و با انتخاب آلیاژ مناسب در هر شرایطی قابل استفاده است.
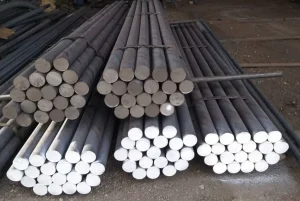
تولید کنندگان فولاد
به طور کلی فولاد از ترکیب آهن و کربن و عناصر مختلف دیگر مانند نیکل، منیزیم، منگنز و … ساخته می شود که درصد کربن در آن تا 2.1 درصد متغیر است. مهمترین عنصر در این آلیاژ آهن است، بنابراین اگر میزان آهن موجود در این آلیاژ کمتر از 50 درصد باشد، این آلیاژ دیگر فولاد نیست. علاوه بر این، اگر با آلیاژ آهن-کربن مواجه شدید که حاوی بیش از این مقدار کربن است، آن آلیاژ فولاد نیست بلکه چدن است.
پرمصرف ترین آلیاژ صنعتی
یکی از مهمترین آلیاژهای تولید شده توسط بشر در طول تاریخ بدون شک فولاد است. امروزه این آلیاژ پرمصرف ترین آلیاژ صنعتی در جهان است و کمتر صنعتی است که فولاد تاثیر مستقیمی بر روی آن نداشته باشد. آغاز صنعت فولاد در ایران به چهارده قرن قبل از میلاد برمی گردد، اما توسعه و گسترش این صنعت در قرن اخیر اتفاق افتاده است.
خواص و ویژگی های فولاد چیست؟
با شنیدن نام فولاد اولین چیزی که به ذهن می رسد مقاومت بسیار بالای این آلیاژ است، اما این نکته به تنهایی دلیل کافی برای این حجم مصرف فولاد در صنعت نیست، بنابراین در نهایت خواص فولاد را بیان کنید. که باعث می شود این آلیاژ به پرمصرف ترین آلیاژ در جهان تبدیل شود، در مورد آن صحبت خواهیم کرد:
1- استحکام کششی بسیار بالایی دارد و نیروهای وارده را به خوبی تحمل می کند.
2- انعطاف پذیری بالا که این آلیاژ را بسیار چکش خوار می کند.
3- در برابر خوردگی بسیار مقاوم است.
4- یدید نقطه ذوب و چگالی بسیار بالایی دارد.
5- درخشندگی زیادی دارد.
6- فراوانی عناصر تشکیل دهنده و هزینه پایین تولید یکی از مهمترین دلایل استفاده گسترده از این آلیاژ در صنعت می باشد.
علاوه بر نکات ذکر شده، یکی از مهمترین خواص فولاد این است که از طریق عملیات حرارتی می توان خواص مختلفی به این آلیاژ داد و آن را برای مصارف مورد نظر سفارشی کرد.
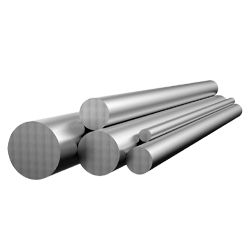
فرآیند تولید فولاد به چند دسته تقسیم می شود؟
همانطور که گفته شد، فولادسازی هزاران سال به طور سنتی انجام می شد، اما فرآیند فولادسازی در قرن چهاردهم تجاری شد. در ابتدا وقتی صنعتگران به اهمیت فولاد پی بردند از روش های سنتی برای تولید فولاد استفاده کردند اما در قرن نوزدهم با استفاده از تکنولوژی توانستند راه های جدیدی برای تولید این آلیاژ کاربردی بیابند که تحول بزرگی در این صنعت ایجاد کرد.
امروزه فرآیندهای تولید فولاد به دو بخش تقسیم می شوند:
1- فرآیندهای اولیه:
این فرآیندها به دو صورت انجام می شود:
فولادسازی به روش اکسیژن قلیایی (فولادسازی با اکسیژن پایه)
این روش اساس فرآیند فولادسازی است که در آن اکسیژن به چدن پرکربن تزریق می شود و با کاهش کربن موجود در چدن، آن را به فولاد تبدیل می کند. دلیل قلیایی نامیدن این روش ماهیت شیمیایی مواد نسوز این فرآیند مانند اکسید کلسیم و اکسید منیزیم است.
رابرت دورر
این روش توسط رابرت دورر در اواسط قرن بیستم اجرا شد و انقلابی را در زمینه تولید فولاد رقم زد که میزان تولید فولاد را به شدت افزایش داد. در این روش اکسیژن با خلوص بالا با فلز منتقل شده و با کربن و سایر عناصر ترکیب شده و آنها را از آلیاژ خارج می کند. آهک را در تمام مدت دمیدن اکسیژن به آلیاژ اضافه می کنیم تا ناخالصی ها را از آلیاژ نهایی جدا کنیم. پس از جدا شدن ناخالصی، آلیاژ مذاب به داخل بوته ریخته می شود تا فرآیند ثانویه انجام شود.
فولادسازی با کوره قوس الکتریکی
در این روش از ضایعات و آهن بازیافتی مستقیماً برای تولید فولاد استفاده می شود. در این روش ضایعات فلزی و آهن بازیافتی با استفاده از قوس الکتریکی در کوره ذوب می شوند. برای کمک به ذوب آهن موجود، گاهی اوقات از مشعل های گازی در کوره استفاده می شود. این کوره ها ظرفیت تولید بیش از 100 تن فولاد در ساعت را دارند. از این فرآیند برای تولید آلیاژهای باکیفیت مانند فولاد ضد زنگ و فولاد کم آلیاژ استفاده می شود، دلیل آن این است که در این فرآیند می توانید کنترل دقیقی بر میزان ناخالصی ها و ساختار شیمیایی فولاد تشکیل شده داشته باشید.
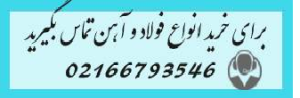
القای جریان الکتریکی
مکانیسم کار در فرآیند فولادسازی کوره قوس الکتریکی به این صورت است که سه الکترود گرافیتی در اطراف کرکره هایی با سقف متحرک قرار دارند. آهن قراضه از بالا و با سقف در یک طرف به کوره اضافه می شود و پس از پر شدن کوره، سقف بسته می شود و الکترودها زیر کوره قرار می گیرند. با القای جریان الکتریکی، قوس الکتریکی ایجاد می شود که حرارت شدیدی ایجاد می کند که بقایای آهن را ذوب می کند و پس از افزودن آهک و اکسیژن، نمونه برداری انجام می شود و آلیاژ مذاب تولید شده برای فرآیند ثانویه که انجام می شود وارد بوته می شود. می تواند اجرا کند.
2- فرآیندهای ثانویه
در این مرحله بسته به نوع فولاد مورد نیاز، عملیات حرارتی مناسب روی آلیاژ داخل دیگ انجام می شود که ممکن است شامل افزودن آرگون، حذف اکسیژن، تزریق پودر و … باشد. برای به دست آوردن فولاد با کیفیت بالا لازم است چندین مورد از این عملیات ترکیب شود.
تولید کنندگان فولاد-تولید کنندگان فولاد-تولید کنندگان فولاد-تولید کنندگان فولاد-تولید کنندگان فولاد-تولید کنندگان فولاد-تولید کنندگان فولاد-تولید کنندگان فولاد-تولید کنندگان فولاد-تولید کنندگان فولاد-تولید کنندگان فولاد-تولید کنندگان فولاد-تولید کنندگان فولاد-تولید کنندگان فولاد-تولید کنندگان فولاد-تولید کنندگان فولاد-